Ronan Collins, Head of Project Information Management, Gamuda
Nick Morecock, BIM Manager, MMC Gamuda,
Original Article is published on the Civil Engineering Surveyor magazine here Reinventing Surveying.
Author – Abigail Tomkins
Our surveyors are our winning team’ was the caption that closed a presentation by MMC Gamuda at October’s Year in Infrastructure conference. It proved to be correct, as the contractor’s work on the Klang Valley Mass Rapid Transit (KVMRT) project in Kuala Lumpur won the award for reality modelling for its use of unmanned aerial systems (UAS). The use of UAS has ‘reinvented surveying’ as Ronan Collins, head of project information management for Gamuda, describes it.
KVMRT is an integrated public transport system involving the construction of two new metro lines. The project was approved by the Malaysian government in December 2010 and the first MRT line, from Sungai Buloh to Kajang (SBK) opened in 2017, covering a distance of 51km with 31 stations. The 36-station second line from Sungai Buloh to Serdang and Putrajaya (SSP) is currently under construction and will cover 52.2km, including 13.5km of track and 11 stations underground
MMC Gamuda, a 50:50 joint venture between MMC Corporation Berhad and Gamuda Berhad, is the turnkey contractor for the underground section, which is split across 17 individual construction sites in urban Kuala Lumpur. Level 2 building information modelling (BIM) standards have been adhered to throughout, and continuous surveying has become an integral feed into the common data environment (CDE). Abigail Tomkins met Ronan Collins and Gamuda’s BIM manager Nick Morecock to find out more about the use of surveying technology on Malaysia’s mega-project.
Did surveying need reinventing?
Ronan Collins: We call it ‘reinventing surveying’ because the use of UAS has completely revolutionised surveying for us. The original intention was to use UAS surveys to create a geospatial reference model that could validate the BIM design data.
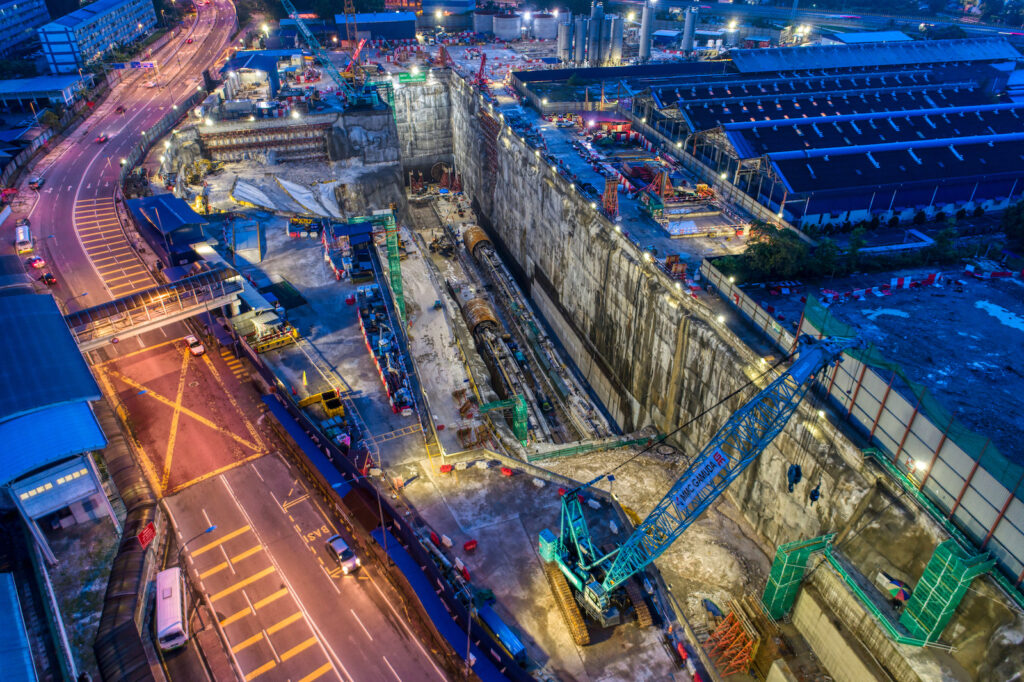
That theory was proved right, and we dramatically enhanced our designer’s understanding of the site constraints and context. We then decided to keep using the technology for continuous survey as construction works started. One UAS survey takes about two hours of flight and approximately a half-day of post-processing per site. We’re collecting hundreds of high-resolution images along the project corridor, and then use ContextCapture photogrammetry software to convert them to a 3D site mesh. We also use the orthophotos within GIS to create a photo- realistic site representation.
Nick Morecock: It’s really democratised access to site surveys and enabled our teams to have regular visibility of the sites without the need for extensive visits. That bird’s-eye view of progress with context and sense of proportionality has been vital in decision making. Once we started delivering the models via our in-house GIS platform, demand for them grew.
Did the surveyors need reinventing?
Nick Morecock: As we have survey teams across all our 17 sites, we needed a strategy to introduce UAS surveying. The whole process took about 12 months. At first we engaged an external company
on a contract to fly the sites, while we purchased the DGI UAS and cameras,
and got our surveyors trained up. At the end of the service contract, we were able to run a pilot on one site with our own surveyors, and then scale it up. We’ve now got 30 trained and certified UAS pilots and spotters.
Ronan Collins: It is the surveyors themselves who have developed the use of UAS through their own initiative. Our surveyors also work on upcoming projects, as well as the underground SSP Line. Two of our team flew a 50km alignment for a future rail project and created a ContextCapture model of the whole stretch – in just six weeks! That’s only one example of where when you have the tools and the processes, innovation will flourish. However, as is the case with surveyors, they don’t always shout about this innovation. As an industry we need to champion this more.
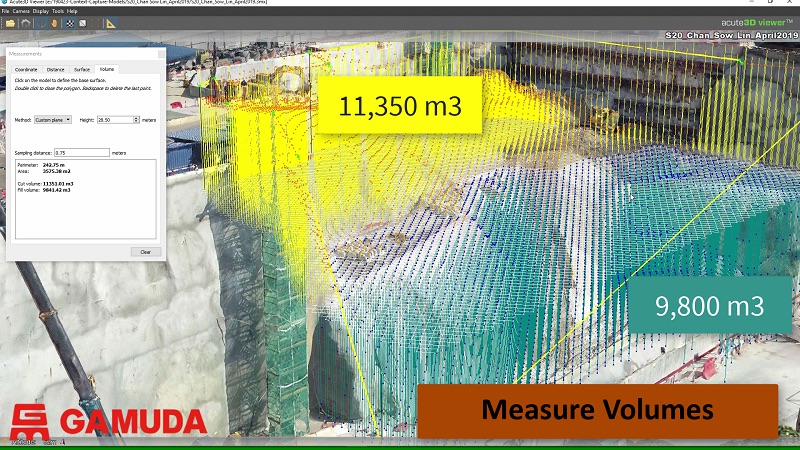
What are the flying regulations in Malaysia?
Ronan Collins: Malaysian law prohibits the collection of images from an elevated vehicle. The government security agency needs to be aware of every flight we make and we are required to submit copies of any images we take. We also have to contact the Department of Survey and Mapping Malaysia (JUPEM) and Civil Aviation Authority of Malaysia (CAAM) to issue a notice to airmen every time we fly.
Nick Morecock: UAS are actually really difficult to fly – it is so easy to lose track of which way you are going, and become disoriented. We have created a policy at Gamuda that states if you want to operate UAS on a Gamuda project, you need to have been through our training process and commit to following our set procedures every time you fly. UAS flying is not the main job of our surveyors. Their every-day work is setting out, taking measurements and creating ground control points, so when they do survey with UAS, we need those steps and procedures to remind them and keep this a safe survey practice. Every flight we do has at least one pilot and one spotter present.
Has opening up the models to the wider project team impacted work on site?
Ronan Collins: One of our subcontractors was carrying out an excavation and piled the material along an embankment at the top of the D-wall. It wasn’t anything unusual – it’s a typical place to put it. However, once we uploaded our regular site model to the cloud one of the consulting engineers saw it and immediately contacted the site. He’d designed that D-wall, and hadn’t accounted for the surcharge from the additional material that was being added.
It was a situation that no-one could have predicted, and could have led to unexpected loads on the D-wall, but the sharing of the survey model alerted the engineers to the potential issues. Progress reports are nothing new, but the extra context from the UAS visualisation is transformative.
Nick Morecock: We are now exploring potential uses of UAS to reduce risk in difficult to access or dangerous locations. When we experience a wall collapse, we’ll send in the UAS first to assess the risk before any workers go in.
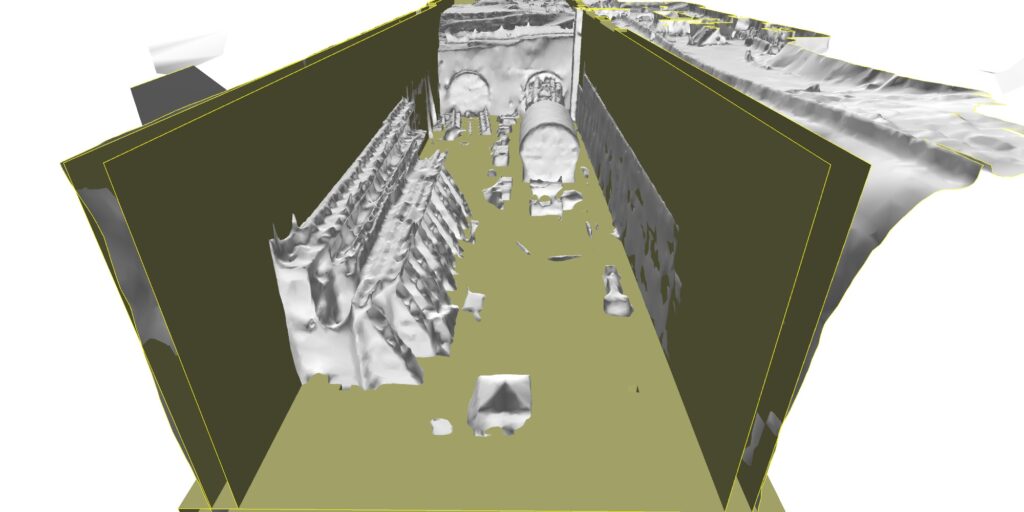
Are the geospatial models being used by the commercial team?
Nick Morecock: We are currently undertaking some pilot studies
to engage with our commercial managers to see how they can leverage the models for quantification and sub-contractor progress assessments. This additional use of the survey models has the potential for time savings and improved accuracy.
Ronan Collins: Continuous survey provides a record of progress that can be measured, especially if you have a model for every week. A photograph speaks a thousand words. You can go back and see exactly how many excavators were on site and when which crane arrived where.
You can validate subcontractor claims with a definitive answer, rather than a subjective one.
The models are going to be a huge asset to contractors, but there are ownership issues around the data that need to be worked out first. This is one area where contracts need to catch up with technology.
Also, commercial staff need to catch up with what is available to them, so they can start asking questions and driving survey requirements. Surveyors know what can be done, our challenge now is to get other teams to be able to use it.
What software and systems are you working with?
Nick Morecock: Cloud-based systems are now the industry norm. The cloud helps massively with document control. Before the cloud, we’d send files in and out as email attachments for being worked on by a single user at a time – ultimately ending up with a mess of duplicate titles, formats and file content. Moving to cloud computing has centralised, structured and controlled document and data storage for us, and we know we have that data backed- up for retrieval.
For the CDE we use Viewpoint for Projects. This was a client requirement and it also supports our BIM level 2 certification.
BIMcollab is our cloud based design and construction issue tracker. The program centralises all the issues on the project, assigns them to team members and sets deadlines. It has removed the need for conventional communication tools such as email and Whatsapp, which were incredibly difficult to track and audit.
We use Viewpoint’s Fieldview for tracking and reporting site-based construction activity. It combines 3D model data with planning data in an internal database that the site engineer can use to mark the status of on-site activities. This data can then be leveraged by our data analytic tool, IBM Cognos, for real-time monitoring of multiple construction activities across multiple sites.
Ronan Collins:
We’ve embraced level 2 BIM standards, which has meant our digital data needs to be structured and managed effectively. Clients are becoming more savvy and being ever more explicit with their project requirements, often defining what deliverables they need, what digital processes should be used to deliver them, when they need to be delivered and how this information should be exchanged.
These requirements in the future will be more dependant on contractors being capable not only in digital technology, but that they can demonstrate explicit compliance with approved information management standards
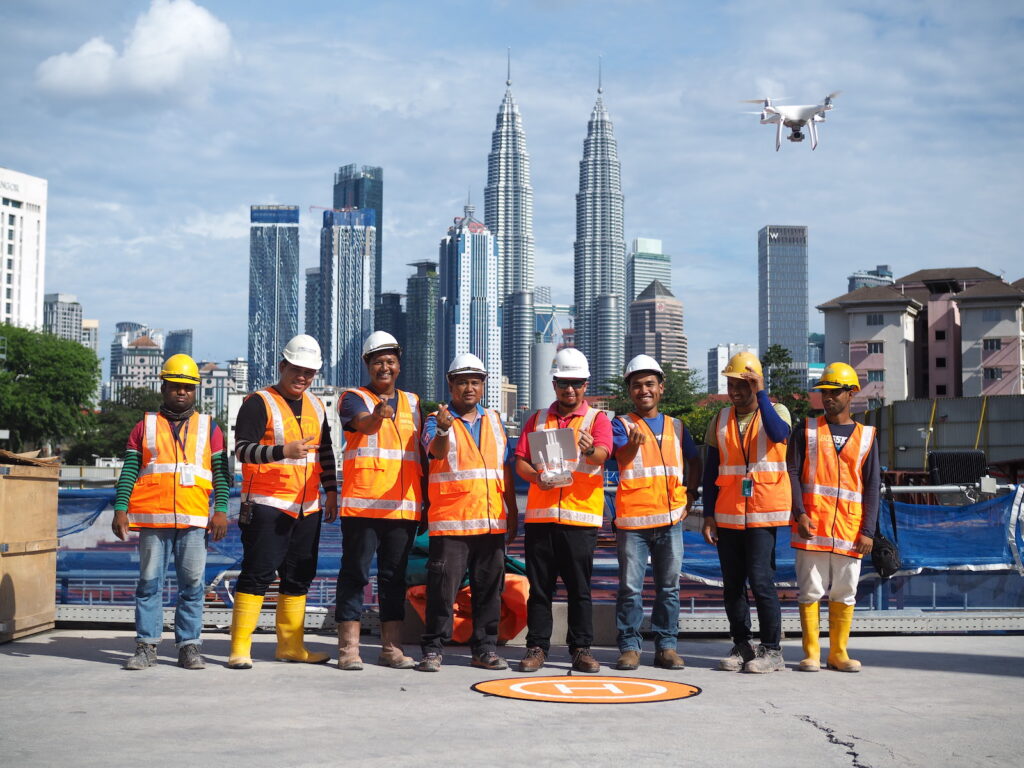
How has having an in-house GIS team been of benefit?
Nick Morecock:
GIS expertise has been vital in developing and sharing innovation on the SSP project. It was our own GIS team who figured out how to take the mesh out of ContextCapture, run it through web XML and put it on the cloud to deliver it via a URL with a pass code. That simplicity opened up our survey work to the project team. The project manager was so impressed with the monthly model, he’s now asked for it weekly.
Historically, GIS has not necessarily been considered a huge benefit to a contractor, but developing and retaining those skills on this project, means we will have the technical knowledge to develop comprehensive GIS platform solutions for any new project or client. It’s a valuable asset to have.
What other tech innovation is being trialled on the SSP Line?
Ronan Collins:
We’ve seen major developments in the tunnelling itself. Gamuda runs a programme where it sponsors students through university, with a job placement at the end. Two of our graduates, both in their mid-20s, one with a first-class electrical engineering degree, the other a first-class mechanical engineering degree, are now back home in Malaysia working on the SSP Line after being educated in the UK. They have what they call a ‘little coding project’, which is essentially writing algorithms to drive tunnelling machines. The productivity gains from this have been immense. Normally, you’ll find someone with 20 years of experience at the helm of the tunnelling machines, but they will still experience drift.
Often it can be hours before we’ve detected that the machine is drifting – this ‘little coding project’ instantaneously corrects the machine based on all the data it is getting. We hit a problem when we brought in some newer machines and the software wouldn’t work, but the same two graduates went back and developed version 2 of their program in a matter of days. We now have 12 TBMs being run by an algorithm, written by kids that we put through university. It is completely mind bending; one, that we can achieve such levels of innovation, and two, that we are not shouting about this to the wider industry.
What’s coming next?
Ronan Collins: Surveying site progress is going to really come into its own in the next few years. With continuous survey, we can correlate the numbers of machines and people on site against the progress of the excavation and start to get patterns about our productivity. It’s early days, but we’re moving to more real-time data assessment of job sites, rather than relying on boots on the ground being 100% aware of what’s going on.
The accuracy from programs like ContextCapture is getting better and better.
As long as you’ve got the ground control points and good camera resolution, you can now combine data from UAS imagery, handheld photographs, and terrestrial laser scanning to generate much more accurate meshes. It’s taking a number of very large data sets and creating one detailed, smaller and more useful model. The demand for that service is going to be exponential. We’ve already got engineers asking for a 3D mesh so they can do their measurement calculations.
Nick Morecock: We are also looking at machine learning in relation to deformation monitoring. Where we experienced a wall collapse, we’ll be looking at the previous surveys and see how the crack developed. If we can then ‘teach’ the software to recognise that and flag up similar cracks in the future, we will have a much safer site.
What’s the future for rail in Malaysia?
Ronan Collins: We’re on track for completion of the SSP Line in 2022. The project is around 58% complete, with tunnelling 80% done. The tunnelling is the linchpin of everything.
Obviously, we can trip, like Crossrail, but we think we’ve done enough with the design management and coordination management to avoid any disasters. There’ll be plenty of people going through masters courses for the next 15 years doing a thesis on Crossrail and what went wrong!
Nick Morecock: Our worry is losing the people and the skills that have been nurtured on this project. The Malaysian government is looking into Line 3 of the KVMRT, but when that gets the go-ahead is unknown. As is always the risk with contractors, if the next job isn’t lined up, then your workers will move on. We’ve developed some great skills and processes on this project that we can export elsewhere, but we’re hoping that Line 3 gets the go-ahead and that we’ll be the ones who are building it.
Ronan Collins, Head of Project Information Management, Gamuda and
Nick Morecock, BIM Manager, MMC Gamuda, were talking to Abigail Tomkins